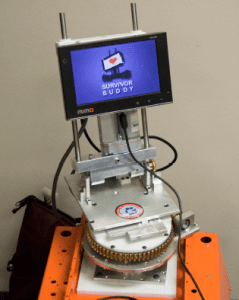
The Survivor Buddy project is a joint project between Texas A&M and Stanford Universities, whose major goals include developing a web-enabled search and rescue robot (Survivor Buddy) and using that platform to further understanding of using computers and robots as a social medium. The project is led by Dr. Robin Murphy from Texas A&M, a world leader in robot assisted search and rescue, and Dr. Clifford Nass from Stanford, a leading expert in the psychology of human computer interaction.
The project began as a response to the attacks on the World Trade Center, which made Dr. Murphy begin to research ways a robot could be used effectively not only to extract information from victims but as a source of comfort as well. Comforting and sometimes entertaining a victim in the time between locating them and extracting them was further highlighted first by the Beaconsfield Mine collapse and then later by the 2010 Copiapo mining accident.
The original Survivor Buddy (Survivor Buddy 1.0) was a web-enabled touchscreen robotic “head,” constructed by a team of students at Texas A&M in August 2009. It is designed to be mounted on top of a mobile robot to and serve as an extension of that robots capabilities. The timing of the construction was planned so that it would be ready just in time to film an episode of the PBS Show SciGirls entitled “Robots to the Rescue!” This robot went on to be declared one of Popular Science’s Best of What’s New for the year 2009. Although this robot was capable of interacting socially and utilizing affect, the team felt, due to the time crunch to prepare for filming, there were areas for improvement.
The following sections deal with the redesign of Survivor Buddy and my involvement as lead designer, mechanical engineer, and electrical engineer for the new robot. For a much more detailed account, my paper from ICRA 2011 which documented the design process is available to download here: A Multi-Disciplinary Design Process for Affective Robots: Case Study of Survivor Buddy 2.0
As the most mechanically inclined member of the Survivor Buddy team, I was chosen to lead the electro-mechanical redesign of Survivor Buddy in January 2010, and I began working on the project full time that June . The initial prototypes for what would become Survivor Buddy 2.0 were made prior to my full time commitment to the Survivor Buddy project and as a result they were constructed from whatever parts I had lying around or anything I could afford on a college budget, while using borrowed tools.
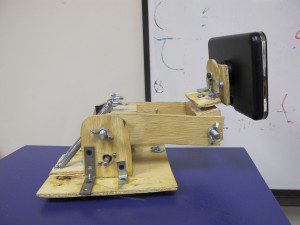
SB 1.1 was built using scraps from a previous robotics project and allowed the other members of the team to evaluate the new form factor and how the new version would move.
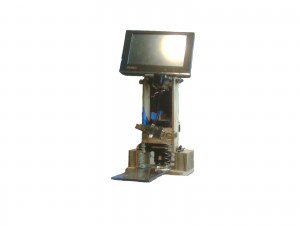
SB 1.2 changed a couple attributes of the previous design, as we had now selected motors for the robot, and I adjusted the design to best utilize the dimensions of the motors. Another key change was the removal of the base rotation joint as we had determined it was unnecessary and should be cut to save space and weight.
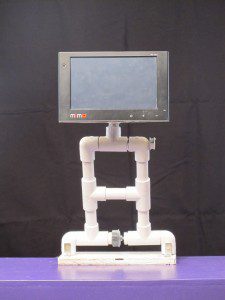
SB 1.3 was the final non-functional prototype and was a bit of a departure from the other prototypes in terms of design and materials used. The PVC allowed for a build time of less than an hour and this prototype was a favorite of the animators and theater design personnel that were brought on to make the robot feel more friendly. This design has a wider main arm/neck than any previous prototype as well as being the first design to not include a spring counterbalance system.

Design Version 1.4
Survivor Buddy 2.0 is based on design iteration 1.4 and the finished robot is shown above. The final build materials were aluminum and carbon fiber which I hand machined in a wood shop due to lack of availability of machine shop time. The final design ended up being a vast improvement over Survivor Buddy 1.0 in every important measurable. The second generation design was not only under a quarter of the weight of the original, but it also cost half the price, while having quicker joint velocities and the ability to more accurately convey affect.